风险理念与质量生产管理实务
——风险重在预防
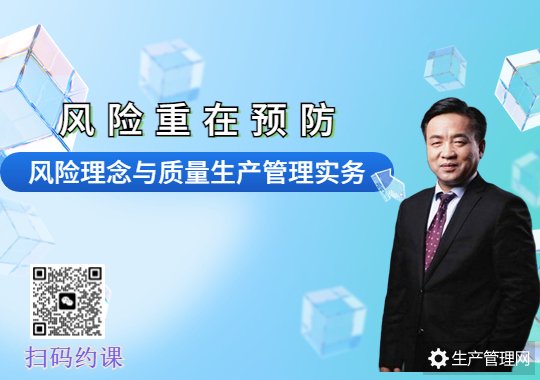
课程背景:
企业高层管理人员常常感到困惑:企业规模大了,员工多了,利润反而降低了。实践证明,企业内部运作管理中40%的成本源于管理和产品的过失及浪费,员工缺乏风险意识与改善意识和改善方法,缺少改善的动力。不能发现现场存在的各种质量与生产风险,导致发生很多质量不良导致的浪费现象,如何培养企业管理人员的风险意识并明确管理措施,并激发现场员工的改善和创新意识,从企业管理的浪费挖掘目标利润,没有不赚钱的企业。
课程收益:
● 树立正确的质量理念与风险的理念;掌握运用产品先期策划的流程与方法识别质量风险;
● 掌握产品缺陷的分析与控制方法与工具来识别评估质量风险;
● 根据质量控制风险分析结果正确编写各种检验标准的方法;
● 根据生产现场风险分析结果来明确运行控制的技巧与方法;
● 根据质量风险评估结果来进行规范质量问题的处理步骤与方法;
● 掌握质量风险降低的工具与方法,了解如何评价质量体系风险控制的有效性技巧与方法;
● 根据风险管理理念梳理优化本公司的运营流程;把风险控制的方法与技巧运用到公司各部门运作中去,减少质量风险;
● 掌握现场作业标准化,目视化管理以及现场5S管理推行等核心工具的运用方法和技巧;
● 帮助学员有效认识并解决生产现场实际工作难题,提升现场管理者的现场管理能力;
● 从客户的角度出发,认识过程中的浪费,并持续消除浪费;采用精益化的生产系统,提高过程的循环效率及客户满意率。
课程亮点:
▲流程化:每个模块都由讲解、案例讨论与练习、老师点评三大流程组成,确保学员课程学习效果。
▲工具化:全程干货,每个模块提供相应表格、流程与具体操作技巧方法等关键工具。
▲轻松化:教学体验活动新颖、愉悦,寓教于乐,确保学员在快乐轻松学习气氛中提升与进步。
▲标准化:符合成人教学原理以及国际流行教学设计,让学员听得懂、记得牢、做得到。
课程时间:2-3天,6小时/天
课程对象:企业中高层,质量经理,生产主管,质量管理人员、工艺管理人员、部门主管及相关质量管理体系人员。
课程方式:
▲.理论联系实际:实战理论讲授+实战案例剖析+实际工作研讨
▲.现场输出成果:实际问题解决+现场成果输出+实战课题转换
▲.持续跟踪辅导:确立课题项目+创建改进团队+持续跟踪辅导
![]() |
课程模型与原理:
课程大纲
模块一:质量管理风险与国际标准
第一讲:质量意识与质量风险
一、质量基本概念
研讨:质量是检验出来的吗?产品质量是制造出来的吗?发现质量异常应该如何处理?
不接受不良品、不制造不良品、不交付不良品
二、质量专家介绍及质量发展进展
1. 质量管理中的“三不”政策
2. 质量管理专家如何说质量
分析:现阶段质量管理六大误区
团队案例分析+小组发表与点评:通过哪些活动开展,可以影响企业高层?中层?基层人员?从而塑造优秀的质量文化案例分析与讨论
主要解决问题与成果输出:质量管理各自为政,改变质量管理从“要我做”为“我要做”的自主质量管理模式
三、风险管理概述
1. 风险管理标准
2. 实施风险管理的目的和意义
3. 风险分析
第二讲:国际标准条款与风险管理
一、国际标准条款要求(内部/外部环境)
二、风险评估与管理
1. 明确风险管理过程状况(确定风险准则与原则、确立风险管理框架)
2. 风险管理流程
3. 风险评估(风险评估过程:风险识别、风险分析、风险评价)
4. 风险管理注意事项
案例分析与讨论
团队案例分析+小组发表与点评:风险识别评估与案例分析与讨论
主要解决问题与成果输出:解决企业相关人员不了解风险识别与评估的技巧与方法。
模块二:现场管理风险与FMEA
第一讲:现场浪费与风险管理
一、认识浪费
引入:1)本节讲解企业各级管理人员如何正确理解浪费(什么是价值?什么是浪费?)
2)传统的浪费与现代浪费的定义不同点
3)丰田和美国专家对浪费的定义
二、七种浪费介绍
1. 等待的浪费
2. 搬运的浪费
3. 不良品的浪费
4. 动作的浪费
5. 加工本身的浪费
6. 库存的浪费
7. 过量生产的浪费
团队案例分析+小组发表与点评:找出本公司发生的七大浪费现象并提出改进方法
主要解决问题与成果输出:解决企业相关人员不了解各种浪费产生的影响。
第二讲:风险管理与FMEA
导入:FMEA介绍
一、过程FMEA与风险管理
1. 生产过程管理风险
2. 风险评估准则
3. APQP系统图
4. 设计矩阵表
5. 过程FMEA的构筑
6. 风险评价
7. 可靠性FMEA
案例分析
研讨:如何编织质量控制计划
团队案例分析+小组发表与点评:结合企业产品实际进行PFMEA案例分析练习
主要解决问题与成果输出:不了解产品生产过程中哪些过程产生质量问题的原因?机理?从而缺乏预防问题发生的手段与措施
第三讲:现场管理与风险控制
一、现场人员管理与风险管理
1. 管理:人员出勤状况、员工情绪与士气、确认新员工工作状况
2. 辅导:进行员工教导、培养良好的工作关系、激发员工的积极性、奖励与惩罚员工
二、现场设备管理与风险管理
1. 设备现场管理内容与分类
2. 设备操作管理
3. 设备维护保养
4. 设备履历
三、现场作业管理与风险管理
1. 异常作业的作业工序步骤确认
2. 确认作业标准书的符合性
3. 异常原因分析
4. 修正作业标准书
四、现场材料管理与风险管理
1. 领料管理与材料标识
2. 不良材料确认与原因分析
3. 与相关部门协调处理材料异常
4. 材料需求状况确认
五、现场环境安全管理与风险管理
1. 现场需要的环境
2. 事故理论
3. 如何营造安全安心工作环境
团队案例分析+小组发表与点评:找寻本公司现场管理中问题点并提出改善方案练习
主要解决问题与成果输出:不了解现场存在的问题点以及现场控制的主要影响因素
模块三:现场风险管理核心工具
第一讲:目视化与现场风险管理
一、改善与目视管理
1. 定置管理
2. 定位管理
3. 定量管理
案例分析:标杆企业定置、定位管理---图片分享
二、目视管理方法
引入:形迹管理
案例分析:标杆企业形迹管理---图片分享
分点讲解:目视管理之颜色管理、透明管理、标识管理、识别板、限度样本
第二讲:6S实务与现场风险管理
一、6S介绍与理念(6s的阻力与好处)
二、6S内容与原则
案例分析:标杆企业5S标准---图片分享
三大原则:6S活动原则、6S规划及实施原则、6S日常活动原则
三、6S的各项要义与要求
1. 整理的含义与要求:做好层别管理和发生根源对策
2. 整顿的含义与要求:做好定置管理和消除寻找时间
3. 清扫的含义与要求:日常清扫活动和微小障碍排除
4. 清洁的含义及要求:如何通过管理保持整洁
5. 素养的含义与要求:塑造形象,创建愉快、融洽的职场环境
6. 现场安全管理的要点:做到安全管理零缺陷
团队案例分析+小组发表与点评:员工素养禁忌调查与讨论练习
主要解决问题与成果输出:不了解工作与生活中需要注意的各种事项与禁忌行为,避免发生各种禁忌行为,成为一名有良好素养的员工
第三讲:作业标准化与现场风险管理
一、作业标准化概述
1. 作业标准化文件
2. 标准化的表现与途径
3. 现场标准化作业(SOP)
二、过程识别方法
1. 识别核心过程
2. 识别管理过程
三、标准化作业(SOP)
1. 包含要素、所需要的人员、程序和方法
2. 标准化作业(SOP)的教导:四阶段教导法
3. 标准化作业(SOP)的维护与管理
第四讲:防错法与风险管理
一、防错法与风险管理
1. 失误、错误和缺陷
2. 人的失误一般原因
3. 制造过程常见失误
4. 管理过程的常见失误
5. 防错法的作用
6. 对待失误的三类态度
二、防错法技术与工具
1. 防错思路:消除、替代、简化、检测、防护
2. POKA-YOKE四种模式:有形防错、有序防错、编组与记数防错、信息加强防错
3. 防错检测技术:判断型检测、信息型检测、溯源型检测
4. 防错装置:防错装置的水平、日常检测装置
分享:防错法十大原理
团队案例分析+小组发表与点评:公司设备管理中防错防呆案例练习
主要解决问题与成果输出:不了解工作中发生的各种错误的原因及如何预防错误发生的措施
模块四:质量实务运用与质量风险
第一讲:质量控制与风险管理
标准:风险评估准则
一、进料检验与风险管理
1. 进料(货)检验和推动免检活动
2. 如何编写进料检验标准
案例分析
二、过程检验与风险管理
1. 过程检验控制方法
2. 过程检验检查点布局
3. 过程检验巡视检查
4. 过程检验质量控制
案例分析
三、成品检验与风险管理
1. 成品检验类型
2. 成品检验标准
3. 成品检验实施
风险评估准则检验标准编制案例练习
主要解决问题与成果输出:不了解各种质量标准编制的具体要求,导致质量控制标准起不到有效控制的作用。
第二讲:用质量成本评价质量运营风险
一、质量成本介绍(任务与阶段)
二、质量成本的定义与分类
1. 分类:预防成本、鉴定成本、外部失败成本、内部失败成本
2. 质量成本的细分
3. 各种质量成本间关系
模块五:质量风险与质量改善
第一讲:质量风险降低改善活动
一、风险问题意识(改善无处不在,PDCA应用)
二、风险降低改善基本原则
1. 认识并消除不合格
2. 质量改善四步法
3. 员工提案改善三步法
4. 多产提案的方法和步骤
三、质量风险改善的基本步骤
明确目标与标准——发现问题——原因分析——确定要解决的问题——拟定对策——做出行动计划——执行行动计划——改善效果确认——标准化管理
模块六:学以致用复盘行动
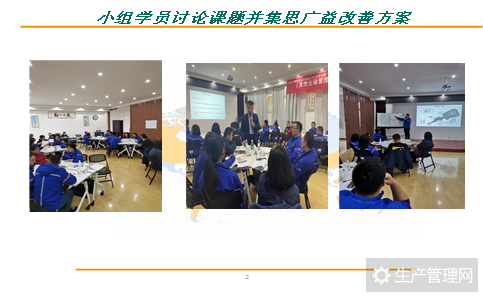
各学习小组总结学习内容,提炼课堂学习心得,完成课程复盘
各小组选择1-2个生产与质量管理中存在的主要风险改善课题,运用企业运营与质量风险管理培训中学习到的各种质量工具,方法设定改善目标与老师,小组人员研讨改善措施与方案,形成小组改善计划。
课题名称 | 改善目标 | 改善措施 | 责任部门 | 开始时间 | 完成时间 | 进度追踪 | 效果确认 |